At BPS Plastics, we work closely with manufacturers across industries to solve problems around space, transport, and load handling. One of the most persistent challenges in shipping and logistics is managing the volume and weight of returnable packaging. That’s where collapsible shipping containers prove their value. These durable, space-saving crates simplify outbound and return shipments for manufacturers under pressure to move parts, products, and materials on tight schedules and budgets.
We design and deliver transport solutions for factories, distribution hubs, and supply chains that need consistency, repeatability, and efficiency. Collapsible shipping containers are central to that strategy.
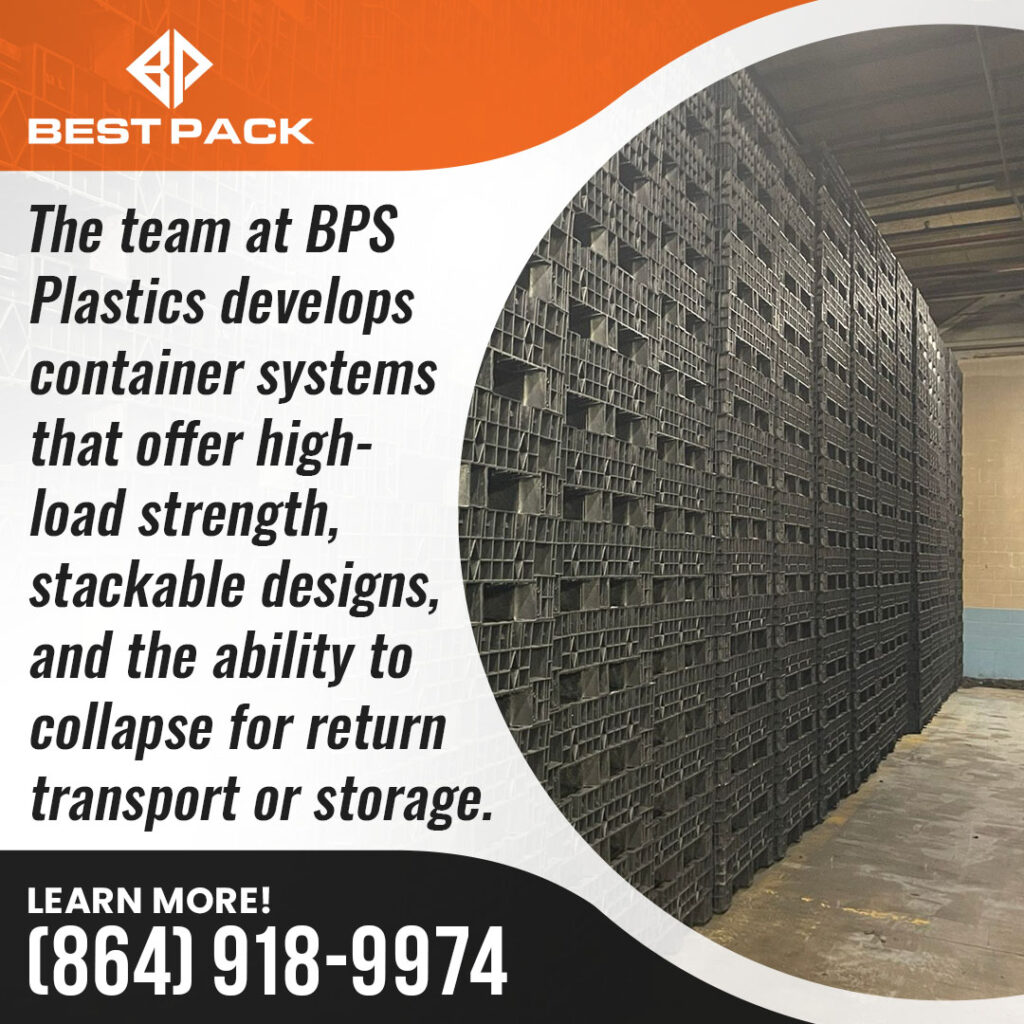
Key Takeaways
1. Collapsible shipping containers reduce return freight costs.
By folding flat after delivery, these containers cut down on return-trip volume, allowing up to 3x more empty units per truck compared to rigid options.
2. Collapsible pallet containers improve load handling speed.
Standardized footprints and compatibility with forklifts, conveyors, and automation help manufacturers move shipments with less manual effort and fewer delays.
3. Collapsible storage containers with lids protect sensitive parts.
Lid-secured models help safeguard electronics, precision parts, and cleanroom materials from dust, impact, and contamination during transport.
4. Reusable containers cut packaging waste and long-term costs.
Switching to collapsible plastic crates reduces cardboard use, dunnage, and shrink wrap while supporting hundreds of reuse cycles across shipments.
5. Container store collapsible crates offer modular flexibility.
These smaller, stackable units work well for internal movement, part picking, and high-turnover inventory handling within manufacturing plants.
Why Load Handling Matters in Manufacturing
Manufacturing systems depend on a steady and timely flow of materials, from raw components to finished goods. Any disruption in this flow, even a small one, can affect the entire production schedule.
Common Flow Disruptions Include:
- Late-arriving parts needed for assembly
- Outbound shipping delays that tie up space and resources
- Slow return of empty containers, especially if they’re bulky or hard to handle
Role of Containers in This Flow
Traditional heavy, rigid containers can hinder rather than help material movement due to their physical limitations:
Disadvantages of Rigid Containers:
- Take up the same space whether full or empty, reducing storage flexibility
- Require more manual or equipment handling due to their weight and size
- Causes inefficiencies in return logistics, especially when shipping them back empty
- Contribute to staging congestion, slowing down workflow in tight production areas
Why Manufacturers Are Changing Their Approach
As operations adopt lean manufacturing principles and tighter delivery schedules, even containers are being scrutinized for efficiency.
What Modern Manufacturers Need:
- Compact, collapsible containers to reduce return freight and floor space usage
- Lightweight and stackable options to speed up loading, unloading, and in-plant movement
- Durable materials that support multiple use cycles with minimal damage
- Flexible container formats for just-in-time delivery systems and frequent product changeovers
By rethinking their packaging and transport systems—including the containers themselves—manufacturers can better support lean, responsive, and scalable production environments.
How Collapsible Shipping Containers Improve Manufacturing Shipments
Collapsible Shipping Containers and collapsible pallet containers meet the demands of modern manufacturing in five key ways:
1. Space Savings During Return Trips
When containers are emptied after delivery, they collapse down to a smaller footprint. This means more empty units fit in the same truck, reducing return freight costs. A single truckload of collapsed crates can carry up to 3x more units than rigid alternatives. According to Market Research Intellect, collapsible containers can reduce storage volume by up to 80%, resulting in fewer return trips and improved logistics efficiency.
2. Consistent Footprints for Automation and Storage
Manufacturing facilities rely on automation. A collapsible pallet container maintains standard base dimensions, which allows it to integrate with conveyor systems, robotic pickers, and automated storage systems without disruption.
3. Reduced Handling Time and Labor Costs
Built-in handholds, lightweight materials, and easy-fold mechanisms reduce the effort required for load/unload cycles. Employees spend less time moving packaging and more time focused on core operational tasks.
4. Improved Durability and Reusability
Collapsible crates are engineered for repeated use. Unlike cardboard or cheap plastic, they don’t degrade after a few cycles. Most can withstand hundreds of uses across multiple shipment legs.
5. Better Protection for Sensitive Parts
Whether it’s electronics, components, or delicate materials, a collapsible storage container with lid adds protection. Many models include interlocking lids or snap-fit options that secure loads during movement.
Use Case: Automotive Manufacturing
In automotive supply chains, thousands of parts move daily between Tier 1 suppliers and assembly plants. A single delay can halt production lines, costing hundreds of thousands of dollars per hour.
By switching to collapsible pallet containers, auto parts manufacturers can reduce their return load trips, lower packaging waste, and increase the floor space available for production.
How Our Crates Support Logistics Efficiency
At BPS Plastics, we engineer containers that meet the daily demands of manufacturing workflows. Our collapsible shipping containers support high stacking, integrate with forklift operations, and come in stack heights suited for domestic and export freight.
Unlike single-use packaging or bulky wood pallets, collapsible crates fold down neatly, reducing volume by up to 70% when empty. This space recovery helps both inbound and outbound shipping logistics.
Standardization Across Supply Chains
Inconsistent packaging causes delays in loading, scanning, and racking. With standardized crates from BPS Plastics, every shipment slot, pallet, and bay can be managed more efficiently. A uniform collapsible pallet container aligns with automation and speeds up scanning and inventory verification.
Standardization also means fewer mismatches, better returns management, and more predictable load planning.
Cost and Sustainability Benefits
Durable, collapsible plastic crates reduce long-term packaging costs. They eliminate the need for shrink wrap, excess dunnage, and disposable cardboard. Some manufacturers have cut packaging spend by 20% after switching to reusable containers.
Reusable crates also reduce waste. According to market research, collapsible container systems can reduce storage and transport costs by up to 30%, making them a cost-effective choice for large-scale shippers.
Types of Collapsible Solutions
- Collapsible Shipping Container
Heavy-duty containers for inter-facility transfers and bulk part movement.
- Collapsible Pallet Container
Designed for export shipments, these containers match international pallet specs and fold flat on return.
- Collapsible Storage Container with Lid
Best for electronics, sensitive assemblies, or cleanroom transit. Lid options reduce contamination and damage.
- Container Store Collapsible Crate
Smaller, modular crates for high-turnover inventory or parts picking within a facility.
- Collapsible Takeout Container
While mostly used in food service, collapsible takeout containers have warehouse applications for cafeteria logistics, internal catering, or lightweight transport needs.
Additional Benefits of Collapsible Crates for Manufacturing Shipments
Integration with Lean Manufacturing Systems
Our collapsible containers are designed with lean manufacturing principles in mind. These systems prioritize waste reduction, space efficiency, and continuous improvement. Traditional packaging often clashes with these priorities—taking up too much floor space, requiring excess handling, or generating waste between production cycles.
A collapsible pallet container fits seamlessly into lean workflows. When not in use, it folds down to free up staging areas, assembly zones, and loading bays. This makes it easier to keep production areas clean and organized, improving workplace safety and process visibility.
In facilities using just-in-time (JIT) systems, packaging must support fast line replenishment without causing inventory overflow. Collapsible shipping containers support precise deliveries and then collapse for return without clogging receiving areas or requiring extra storage.
Cross-Department Efficiency
Shipping is only part of the challenge. Collapsible storage containers with lids also contribute across departments—from receiving to quality control to warehousing. In quality control, secure-lid models help isolate sensitive or quarantined materials, and in storage areas, stackable crates help separate and access parts without unpacking everything on a pallet.
Some customers use collapsible crates for staging daily component kits, utilizing color-coded crates to manage various product variants. When kitting lines change over, the container store collapsible crates can be stacked flat until needed again, freeing up space without complicating material handling.
Customization for Manufacturing Environments
One of the ways we support manufacturers is through customization. Not every crate fits every use. Some require solid walls; others need ventilation. Some customers need label holders, RFID tagging, or color-specific systems to track ownership or route. We offer models that accommodate those variations while retaining foldability and durability.
For example, for electronics manufacturers, we offer collapsible storage container formats with interlocking lids for added part security.
Global Supply Chain Compatibility
Export manufacturers often face differing regulations, pallet standards, and shipment methods. A collapsible pallet container designed to meet international standards helps avoid customs delays and cross-border transport inefficiencies.
Our export-compliant collapsible pallet containers are built to match ISO-standard pallet dimensions and stack safely inside shipping containers. After delivery, they fold flat for efficient backhaul—a critical advantage for companies shipping to and from overseas suppliers or customers.
Extended Product Life and Repair Options
Another strength of collapsible shipping containers is their long service life. Built from impact-resistant polymers, they withstand temperature fluctuations, moisture exposure, and heavy loads. Many models last five to ten years in regular use. It’s a lower-waste, lower-cost approach to managing reusable packaging assets.
How It All Adds Up
Efficient load handling isn’t just about the crates—it’s about what they enable.
- Faster part flows
- Cleaner workspaces
- Lower freight costs
- Safer materials handling
- Fewer labor hours spent prepping or moving packaging
- System integration for lean manufacturing environments
For manufacturers under pressure to deliver more with less, collapsible crates aren’t just helpful—they’re part of the system.
Why Manufacturers Are Shifting Now
Manufacturing isn’t slowing down. Just-in-time and just-in-sequence systems require shipping containers that adapt to fast, frequent shipments. Empty rigid bins slow down processes, increase costs, and waste valuable space.
A shift to collapsible shipping systems reflects an effort to tighten load control, reduce waste, and scale warehouse efficiency without adding square footage. Manufacturers tell us it’s not about spending less—it’s about spending smarter.
Our Role in Your Process
We don’t just supply containers; We partner with operations teams to recommend formats, sizes, and handling systems that align with specific load profiles and floor layouts. Whether you need 100 crates for a small-batch process or 10,000 for a multi-location supply chain, we help map the right solution.
What to Consider When Choosing Collapsible Shipping Containers:
- Load type (bulk, sensitive, heavy)
- Route type (short-haul, LTL, international)
- Return logistics plan
- Storage system compatibility
- Employee handling preferences
- Cycle life and repairability
Our team at BPS Plastics works through these criteria with each customer to match the right product with their operation.
Frequently Asked Questions
1. What is a collapsible shipping container, and how does it help in manufacturing logistics?
A collapsible shipping container is a reusable, foldable container designed for transporting goods efficiently. In manufacturing, it reduces return freight volume, simplifies storage, and lowers handling time across inbound and outbound logistics.
2. How much space can I save using a collapsible shipping container?
Collapsed units can reduce volume by up to 70% compared to rigid containers. This translates to fewer trucks needed for return trips and less warehouse space occupied by empties.
3. Can a collapsible shipping container handle heavy industrial parts?
Yes. Most collapsible shipping containers are engineered for high-load capacities and durability. They are designed to withstand repeated cycles of bulk shipments without structural failure.
4. Are collapsible shipping containers compatible with forklifts and pallet jacks?
Yes. Most models are designed with reinforced bases and fork entry points, making them suitable for standard material handling equipment in manufacturing environments.
5. How do collapsible shipping containers contribute to sustainability in manufacturing?
They reduce the use of disposable packaging like cardboard and shrink wrap, cut down on transport fuel by minimizing volume, and support long-term reuse, lowering overall environmental impact.
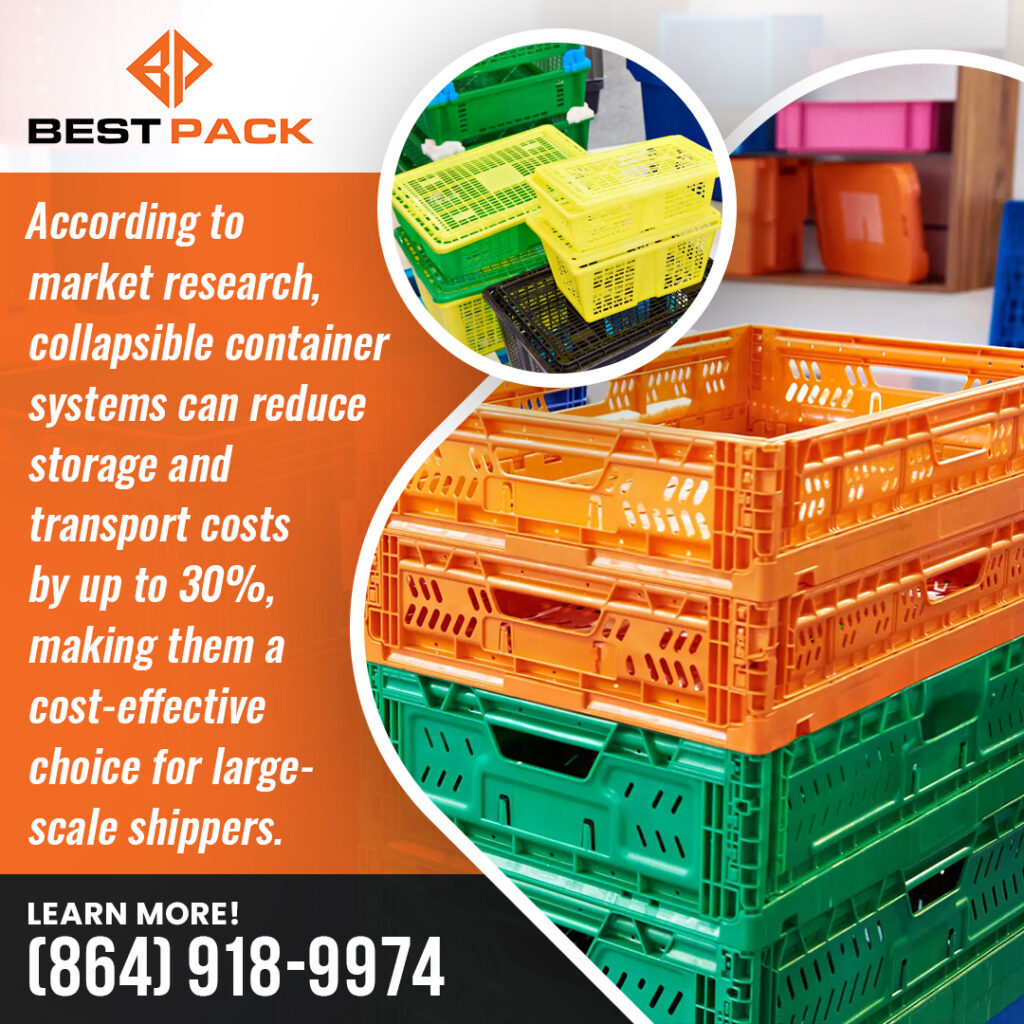
BPS Plastics: Driving the Future of Efficient Manufacturing Packaging
As manufacturing volumes rise, facilities that manage packaging loads efficiently will have an advantage. Collapsible shipping containers and collapsible pallet containers reduce clutter, support faster turnaround, and make each leg of a shipment cycle more productive.
At BPS Plastics, we continue to invest in tooling, materials, and crate formats that keep pace with changes in automation, labor availability, and logistics. Our goal is to build packaging that works harder, lasts longer, and moves smarter for manufacturers everywhere.
Contact Us
To explore our collapsible shipping container options or request a quote, contact us at (864) 918-9974 or email info@bpspackaging.com.
Visit BPS Plastics in Fountain Inn, SC—we’re ready to help you design a smarter, more efficient load-handling system for your manufacturing operations.